The Leading Edge of Injection Molding: Exploring Opportunities with Injection Mold China
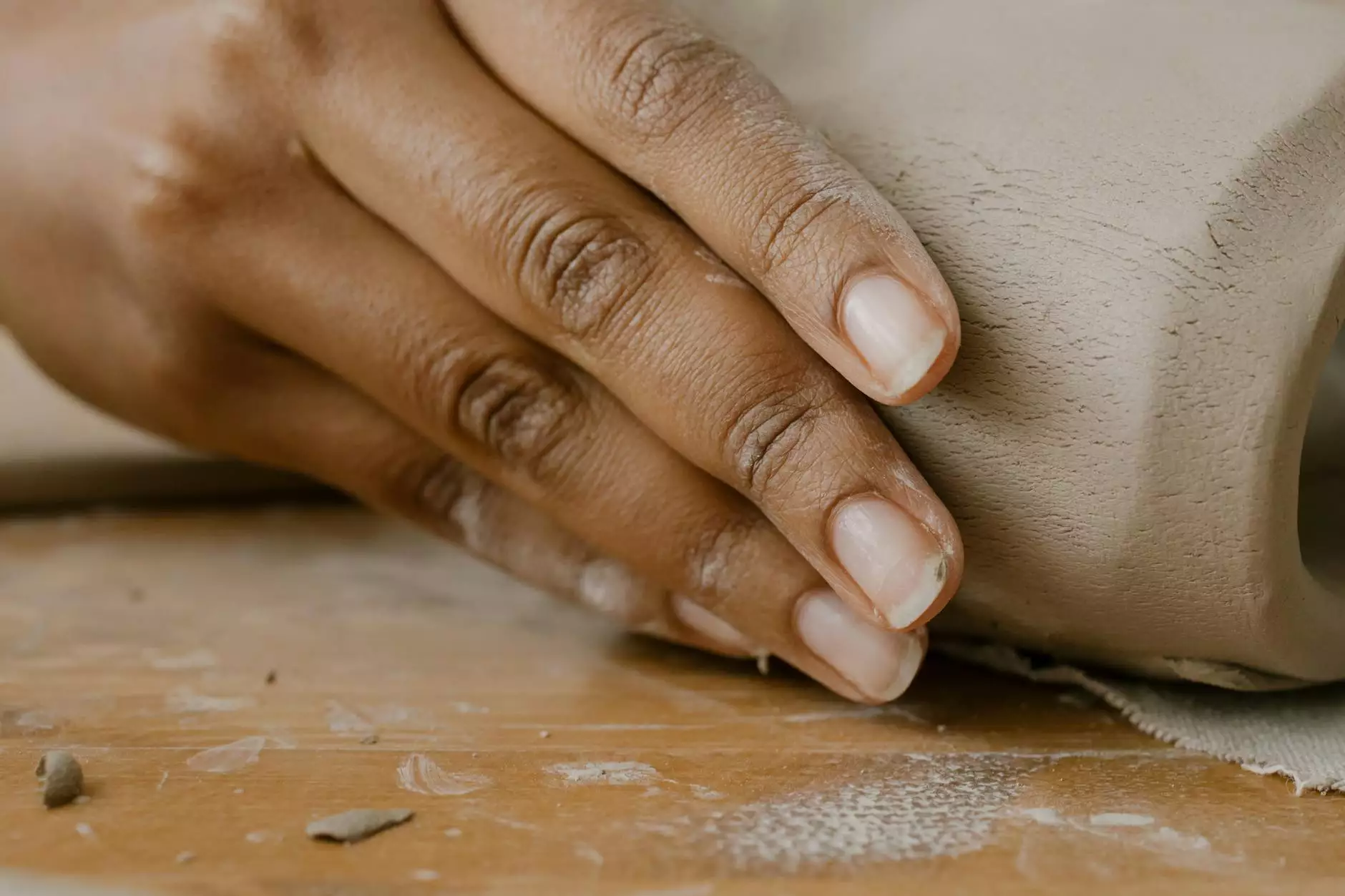
In today’s competitive landscape, businesses are constantly searching for high-quality manufacturing options that can provide both efficiency and durability. One prominent solution that has emerged is injection molding, particularly facilitated by specialized manufacturers in China. With a robust infrastructure and a wealth of experience, these manufacturers are paving the way for businesses worldwide to fulfill their production needs.
Understanding Injection Molding
Injection molding is a manufacturing process used to produce parts by injecting molten material into a mold. This technique is largely utilized for mass production, allowing for the creation of thousands of identical components within short timeframes. Whether your business requires intricate designs or large volumes, injection molding can cater to diverse production requirements.
The Process of Injection Molding
The injection molding process encompasses several vital steps:
- Design Phase: Engineers create the mold design specific to the product requirements.
- Material Selection: Choosing the right type of plastic is crucial; options may include thermoplastics and thermosetting polymers.
- Mold Fabrication: High-precision manufacturing of molds usually occurs using advanced CNC machines.
- Injection Phase: The selected material is heated beyond its melting point and injected into the mold cavity.
- Cooling Stage: The injected material cools and solidifies inside the mold to form the desired shape.
- Demolding: Once cooled, the mold opens, and the finished product is removed.
Why Choose Injection Mold China?
China has established itself as a global leader in plastic injection molding for several reasons:
1. Cost-Effectiveness
One of the primary draws of contracting with manufacturers in China is the remarkable cost-effectiveness. Labor and manufacturing costs are typically lower than in many Western countries. This affordability allows businesses to produce high-quality products at a fraction of the price.
2. Advanced Technology
Chinese manufacturers often invest heavily in cutting-edge technology and machinery. This technological investment ensures that processes are efficient and that products meet international standards. The use of automation in factories further enhances productivity and reduces human error.
3. Skilled Workforce
China boasts a vast pool of skilled workers experienced in the injection molding process. Many of these workers are well-versed in modern manufacturing techniques and can leverage their expertise to meet complex design requirements.
4. Flexibility and Customization
On-demand manufacturing capabilities provide businesses the flexibility to customize products according to their specific requirements. This is particularly beneficial for companies in industries such as automotive, electronics, and consumer goods where unique specifications often apply.
5. Robust Supply Chain
With an established supply chain, Chinese manufacturers can efficiently source raw materials and distribute components globally. This network ensures timely delivery, keeping your production schedule on track.
Choosing the Right Plastic Mold Maker
When seeking an injection mold in China, it is critical to partner with the right plastic mold maker. Consider the following criteria:
- Experience and Reputation: Look for companies with a proven track record in the industry. Customer reviews and testimonials can provide insight into their reliability.
- Quality Assurance: Ensure that the manufacturer adheres to international quality standards. Ask about their quality control processes and certifications.
- Design Capabilities: A manufacturer with robust design capabilities can help refine your ideas and produce superior molds.
- Post-Production Services: Adequate after-sale support and services should be available, including repairs and maintenance of molds.
- Communication: Effective communication is vital for collaboration and ensuring that project requirements are understood and met.
Innovations in Injection Molding
The injection molding industry is continually evolving, with several innovations shaping its future:
1. 3D Printing Integration
Recent advancements in 3D printing technology enable rapid prototyping, allowing for quicker product development cycles. Integrating 3D printing with conventional injection molding can enhance design flexibility and reduce lead times.
2. Sustainable Practices
With growing awareness of environmental sustainability, many manufacturers are adopting eco-friendly practices. This includes using recycled materials and energy-efficient machinery, which not only helps in reducing waste but also lowers operational costs.
3. Smart Manufacturing
The advent of Industry 4.0 has led to the implementation of smart manufacturing practices that utilize IoT and data analytics. This integration allows manufacturers to optimize processes, predict maintenance needs, and improve overall productivity.
Applications of Injection Molding in Various Industries
Injection molding is utilized across a broad spectrum of industries, showcasing its versatility:
1. Automotive Industry
In the automotive sector, injection molding is instrumental in the production of components such as dashboards, interior panels, and clips. The ability to create lightweight and durable parts is advantageous for vehicle performance.
2. Consumer Electronics
Numerous devices, including smartphones and laptops, rely on injection-molded parts. The precision and customization capabilities allow electronic manufacturers to innovate while maintaining cost efficiency.
3. Medical Devices
The medical industry benefits from injection molding through the production of precision components that meet stringent regulatory standards. This includes items such as syringe bodies, surgical instruments, and casings for medical devices.
4. Packaging
Injection molding plays a critical role in the packaging industry by providing durable and cost-effective solutions like bottles, containers, and closures, which are essential for protecting goods during transit.
Conclusion: Embracing the Future of Injection Molding in China
The landscape of injection mold China is rich with potential. As businesses increasingly recognize the advantages of partnering with skilled manufacturers, the momentum toward plastic injection molds continues to grow. With a combination of cost-effectiveness, advanced technology, and a supportive supply chain, the future appears bright for those willing to invest in quality injection molding solutions in China.
Choosing to work with a reputable plastic mold maker not only enhances product quality but also fosters long-term relationships that can withstand the test of time. In an ever-changing global market, leveraging the strengths of Chinese manufacturers can give businesses the competitive edge they need to thrive.