Unveiling the Excellence of a Premier Plastic Injection Molds Supplier in Modern Manufacturing
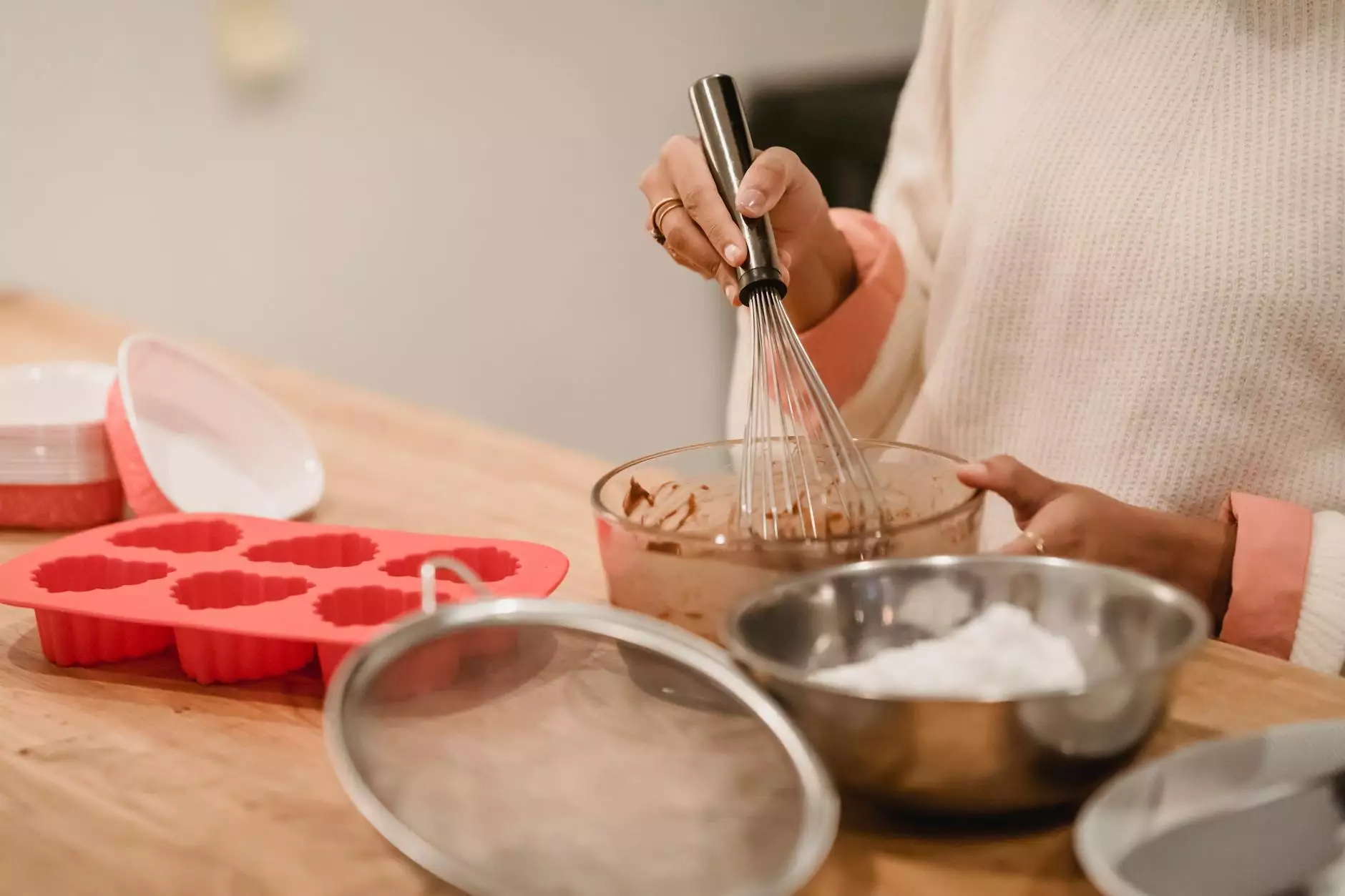
In the realm of manufacturing and industrial production, plastic injection molds stand as the cornerstone of high-quality, precise, and efficient plastic component creation. As a leading plastic injection molds supplier, DeepMould.net exemplifies industry strength, innovation, and unwavering commitment to excellence. Our mastery in creating custom molds has empowered various industries—from automotive to consumer electronics—with reliable, cost-effective solutions that elevate production standards. This comprehensive guide explores the essential facets that make a plastic injection molds supplier indispensable, underscoring why DeepMould.net is your ideal partner in mold manufacturing.
Why Choosing the Right Plastic Injection Molds Supplier Is Critical for Manufacturing Success
The manufacturing sector thrives on precision, efficiency, and innovation. The significance of selecting an experienced plastic injection molds supplier cannot be overstated. A capable supplier ensures that molds meet stringent quality standards, optimize production cycles, and adapt seamlessly to diverse project requirements. Here are compelling reasons why partnering with a proven plastic injection molds supplier like DeepMould.net is fundamental to your manufacturing success:
- High-Quality Molds: Delivering durable, precise, and high-performance molds that withstand rigorous use.
- Customization & Design Flexibility: Tailoring molds to fulfill unique product specifications and complex geometries.
- Cost Efficiency: Reducing production costs through optimized mold design and manufacturing processes.
- Rapid Turnaround Times: Ensuring timely delivery to meet tight project deadlines.
- Technical Expertise & Innovation: Leveraging advanced technology and industry best practices to improve mold performance.
- Exceptional Customer Support: Providing ongoing assistance from design through post-production.
DeepMould.net: Your Premier Plastic Injection Molds Supplier
As a specialized plastic injection molds supplier under the broader umbrella of metal fabricators, DeepMould.net shines through its exceptional capabilities, extensive experience, and unwavering dedication to client satisfaction. Our comprehensive suite of services is designed to meet the diverse needs of modern manufacturing enterprises, supported by advanced machinery, cutting-edge technology, and a team of seasoned engineers.
Our Core Competencies in Plastic Injection Mold Manufacturing
- Custom Mold Design & Engineering: Our process begins with intricate design and engineering, utilizing CAD/CAM software to ensure precise specifications. We collaborate with clients to understand their product requirements, then develop detailed 3D models and prototypes before moving to production.
- State-of-the-Art Manufacturing Facilities: DeepMould.net boasts modern, automated manufacturing facilities equipped with CNC machining, EDM, and high-precision milling machines. This infrastructure guarantees high-quality molds with tight tolerances and fine-detail replication.
- Material Selection & Testing: We employ premium-grade steel, aluminum, and specialty alloys, coupled with rigorous testing protocols to ensure mold longevity and performance under production conditions.
- Precision Machining & Assembly: Our team meticulously assembles molds, adhering to strict quality control standards. This step is vital to ensure flawless operation, easy maintenance, and high repeatability in injection molding processes.
- Prototyping & Sample Production: Before mass production, we create prototype molds and samples for validation, allowing clients to verify design accuracy, functionality, and aesthetic qualities.
- Post-Production Support & Maintenance: Our service extends beyond initial delivery, offering repair, refurbishment, and upgrades to molds, maximizing their lifespan and productivity.
The Process of Manufacturing High-Quality Plastic Injection Molds
Understanding our comprehensive process underscores our commitment to excellence. Here is an overview of the typical steps involved in our mold manufacturing lifecycle:
1. Consultation & Requirement Analysis
Our dedicated engineers work closely with clients to analyze project specifications, product design complexity, desired production volume, and budget considerations. This collaborative approach optimizes the mold design and manufacturing plan.
2. Advanced Design & Simulation
Using sophisticated CAD/CAM software, we develop detailed mold designs, simulating the injection process to identify potential issues like weld lines, sink marks, or incomplete fills. This phase ensures that the final product meets all aesthetic and functional expectations.
3. Prototype & Trial Production
Prototypes enable real-world testing of the mold and the produced parts, allowing for modifications and refinements prior to mass manufacturing. This step minimizes costly reworks and ensures accuracy.
4. Precision Manufacturing
Our skilled technicians employ high-precision equipment for mold fabrication. We focus on exact dimensions, smooth surface finishes, and optimal cavity configuration. Rigorous inspection standards are maintained throughout this phase.
5. Assembly & Tuning
Post-machining, the mold components are assembled with care, followed by testing on injection molding machines. Fine adjustments are made to ensure smooth operation and defect-free production.
6. Delivery & After-Sales Support
Delivered molds undergo comprehensive quality checks before shipment. Our team provides detailed documentation and ongoing support, including maintenance and repair services to sustain high performance over time.
Advantages of Partnering with a Trusted Plastic Injection Molds Supplier
Partnering with an experienced plastic injection molds supplier like DeepMould.net offers distinct advantages that directly impact your manufacturing efficiency and product quality:
- Enhanced Product Quality: Precision molds produce consistent, high-quality parts with excellent surface finishes and dimensional accuracy.
- Cost Savings: Efficient mold design reduces material waste, minimizes cycle times, and lowers overall production costs.
- Increased Production Speed: Well-designed molds enable faster cycle times, accelerating your go-to-market timeline.
- Flexibility & Customization: Our molds can be tailored for complex geometries and small or large production runs, ensuring versatility for various project scales.
- Long-Term Reliability: Durable molds withstand prolonged use, reducing maintenance costs and downtime.
- Technical Support & Innovation: Continuous assistance, technical improvements, and incorporation of new technologies ensure your manufacturing stays competitive.
The Future of Plastic Injection Molds & Innovative Trends
The industry is continuously evolving. As a committed plastic injection molds supplier, DeepMould.net keeps at the forefront of technological advancements. Here are some emerging trends shaping the future:
- Automation & Smart Manufacturing: Incorporation of sensors and IoT devices for real-time monitoring and predictive maintenance, leading to higher efficiency and minimal downtime.
- Rapid Prototyping & 3D Printing: Use of additive manufacturing for quick mold prototypes, enabling faster iterations and cost-effective testing.
- Sustainable Materials & Eco-Friendly Production: Embracing environmentally conscious materials and LEAN manufacturing principles to reduce waste and carbon footprint.
- Advanced Mold Materials: Development of wear-resistant and heat-tolerant alloys to extend mold life and improve performance under demanding conditions.
- Customization & Modular Molds: Flexibility in mold design allows for easy modifications, supporting mass customization and small-batch production trends.
Conclusion: Your Reliable Plastic Injection Molds Supplier for Superior Manufacturing
Choosing the right plastic injection molds supplier is paramount for achieving manufacturing excellence, product consistency, and operational efficiency. DeepMould.net embodies these principles through unparalleled expertise, advanced technology, and dedicated customer service. Our end-to-end solutions—from initial design to post-production support—ensure your projects succeed with high-quality, reliable molds that withstand the test of time.
Be it complex geometries, tight tolerances, or large-scale production, we are committed to providing innovative mold solutions tailored to your unique needs. Partner with DeepMould.net and experience the difference that industry-leading craftsmanship and dedication can make in your manufacturing journey.